Order picking is the process of obtaining the items indicated in the order from the appropriate warehouses. It is the first step in completing a customer's order. It is essential to ensure that the order is completed without difficulty for the following stages to be successful - order packing, shipping, and post-sale activities.
Thanks to an effective order selection process, every order should be filled with the correct item. Every time a consumer receives an incorrect order, the store must deal with the exchange of the goods, handle refund payments, and update stock levels.
Inventory tracking system for small business will help businesses ensure their clients never experience this because it lowers customer satisfaction. This is where an efficient order-picking service comes to the rescue.
3 Types of Order-Picking Systems
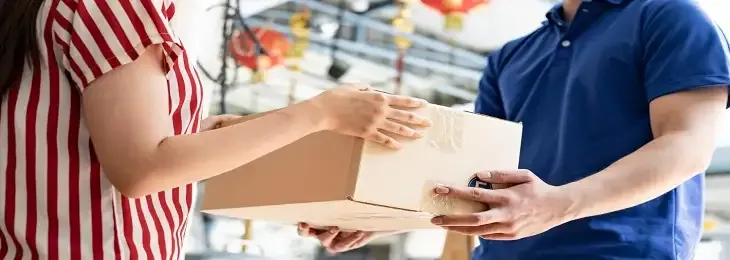
The different types of order-picking systems include Piece Picking, Pallet Picking, and Case Picking. Let's explore the different order-picking systems.
- Piece Picking
When objects are taken out of a warehouse one at a time, this is known as piece picking. This style of choice is frequently used in orders with a larger variety of Stock Keeping Units (SKU) but fewer items per pick.
- Pallet Picking
A wooden platform, a pallet, is used to store a product arrangement at a warehouse. A pallet can carry one large object or multiple smaller ones, depending on its size. Pallet picking is the process of selecting a full pallet's worth of goods and sending them to the packing section.
- Case Picking
Similar to pallet picking, case picking involves selecting only a portion of the pallet and sending it to the packing room. This type of picking is employed when there are many SKUs with few goods per SKU.
Read Also - Understanding Backorders: What They Are, Causes and Solutions
Automated Picking Systems
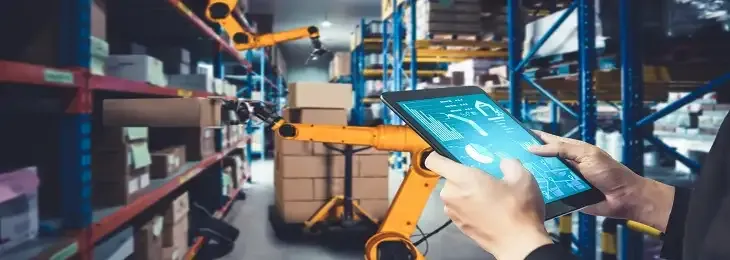
The employment of automated or semi-robotic technologies to assist human pickers in their task is known as an automated warehouse picking system. There are many solutions available for automated warehouse picking. However, the most effective automation system collaborates with your team, rapidly and seamlessly integrates into current warehouse procedures, and enhances order-picking efficiency. Although automated order picking systems can decrease picking routes and save on walking time, they can also interface with your current applications and assist in precise picking and packing. A wide range of businesses, including e-commerce, production, retail, moving goods, alcoholic beverages, medical devices, and more, can make use of it.
Warehouse Order Picking Systems
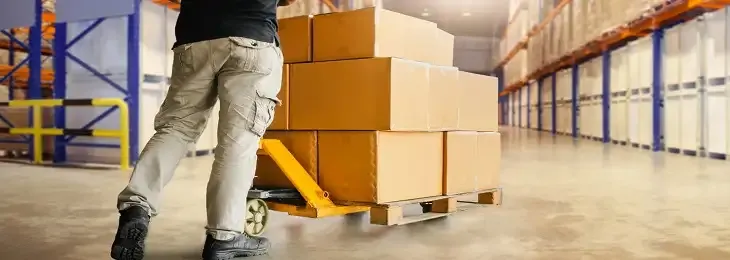
Read Also - What Is Working Capital Management? How to Calculate and Why It's Important
4 Best Combined Order Picking Methods
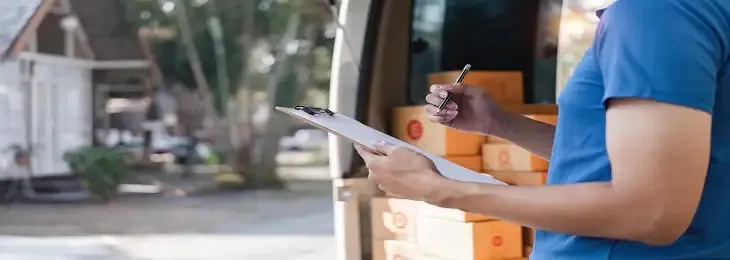
- Single Order Picking
The technique of picking just one order is expected. Order pickers concentrate on finishing one customer order at a time in this method. They frequently make multiple trips around the warehouse collecting stuff. This strategy is best suited for smaller enterprises or warehouses because it is time-consuming.
- Batch Order Picking
Pickers can handle many orders at once by using batch picking. The picker receives several orders to complete and deliver to the packaging station. This approach is perfect for warehouses that handle several orders with a few products apiece. In collaboration with batch picking, the piece-picking type of order-picking system is most commonly used.
- Cluster Order Picking
It is another approach that enables pickers to complete several orders in clusters with a multi-order picking trolley, similar to batch order picking. Pickers can collect numerous things in clusters. It can be according to their shipment dates, place of delivery, or even in clusters of similar items simultaneously using this approach. This technique can reduce the distance pickers have to go inside a warehouse.
- Zone Order Picking
Warehouse zones are used for zone order picking. Businesses frequently combine zone order picking and pick and pass techniques. This technique can help keep the warehouse organized, which is especially beneficial for companies that receive many orders.
Warehouse Order Picking Equipment
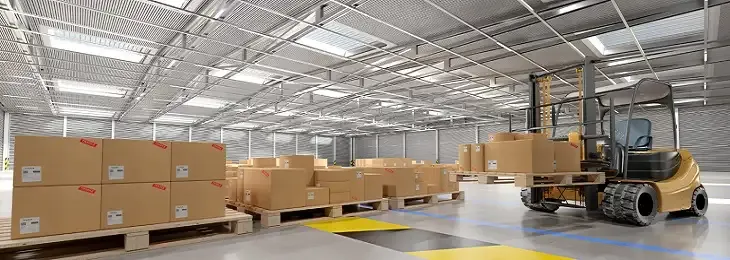
- Mobile collaborative robots assist human employees and direct team members through tasks as they complete them.
- Heavy-duty machinery such as forklifts and pallet jacks are used to manage enormous load capacities.
- Voice-picking tools such as headsets and hands-free systems, give pickers real-time instructions on the next task.
- Intelligent weighing scales assist in minimizing pros and foreseeing changes in shipping costs. Additionally, they stop over and underpacking.
Read Also - Supply Chain Trends for Businesses to Watch in 2023
Warehouse Picking Best Practices
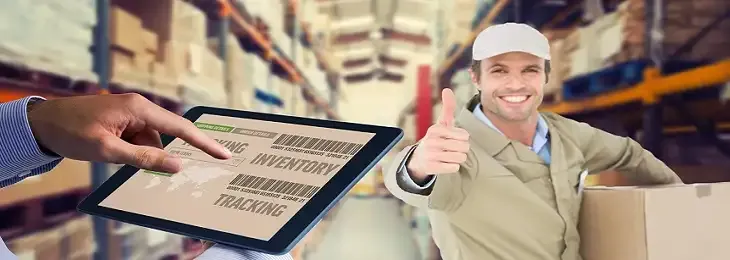
- Set objectives for your level of production
Setting objectives that inspire pickers to complete the most orders in the quickest amount of time without compromising accuracy or safety is important. This can be done by arranging the warehouse to encourage a greater pick density.
- Reduce walking time by carefully planning the warehouse layout
Regular inventory and layout reviews by facility managers are necessary to ensure that SKUs are ideally situated to reduce walking distance. Pickers usually stroll around the warehouse in between picks for a significant amount of "dead time". Pick lists should be arranged to minimize backtracking and enable pickers to finish selects methodically and effectively in the least amount of time.
- Use proper equipment
Reduce the number of hands SKUs come into contact with before being transported to increase productivity and efficiency. Businesses ought to spend money on automated warehouse technology and hands-free equipment.
Read Also - Understanding Consignment Inventory: Definition, Pros, and Cons
Tips for Choosing an Order-Picking System
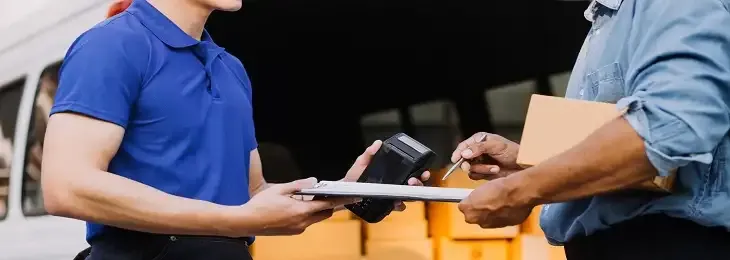
- Think about the number of your goods
The optimal picking system for your warehouse can be determined by the size of your inventory and warehouse. For instance, to ensure accuracy in a small warehouse, you can think about employing the single order picking system. The zone order picking system can assist pickers in managing huge volumes of orders and items if you have a lot of inventory.
- Consider the number of pickers you have
The kind of technology you select may also depend on how many order pickers your company employs. For instance, you might use the zone order picking solutions if you have several pickers.
- Study your data
To assist you in selecting a system, you may also examine the sales statistics of your company. It can be useful to know how many orders your company receives on average, as well as how many things are typically included in each order. This can assist you in selecting a system that can handle the amount and size of orders that your company receives.
Read Also - Producton Routing - Ultimate Guide for SMEs
Why Should Businesses Select the Best Order Picking Services Like TranZact
Supply chain leaders must raise customer satisfaction to defend their company's bottom line in the face of fierce competition and continuously shifting consumer demand. Alongside this, they must focus on lowering the costs of operation. Facility managers must therefore adopt the best picking practices and select the appropriate picking strategy for their facility.
To achieve efficient picking practices and optimize inventory management, it is crucial for facility managers to implement the best system to track inventory. This system plays a pivotal role in ensuring accurate and real-time visibility into stock levels, enabling seamless order fulfillment and reducing the risk of stockouts or overstocking.
They should use the appropriate automated tools and equipment, including order-picking technology like TranZact. TranZact streamlines multi-store inventory management and order processing for SME businesses, saving business time.
FAQs on Order Picking
1. What are the 3 types of order-picking systems?
Order-picking systems for all businesses can be of the following three types:
1. Piece picking
2. Case Picking
3. Pallet Picking
2. What is an automated warehouse picking system?
The employment of automated or semi-robotic technologies to assist human pickers in their task is known as an automated warehouse picking system.
3. What is the advantage of using order-picking services?
Automated order-picking services make the warehouse work more efficient. It helps reduce manual labor costs, ensures zero error rates, and accelerates processes.
4. What is order picking equipment?
Order picking equipment are tools that various warehouse facilities often use to streamline activities, reduce operating costs, and increase efficiency and the accuracy of the work done. These automation technologies can include tools like heavy-duty machinery, voice-picking tools, and mobile collaborative robots.
5. What is order picking?
Order Picking is the process of selecting and gathering items from a warehouse or inventory. It fulfills customer orders and ensures that correct products are picked in the specified quantities.
6. What is the difference between Single Order Packing and Batch Order Packing?
Single Order Packing focuses on completing one customer order at a time, with pickers making multiple trips to collect items. On the other hand, batch order packing allows pickers to handle multiple orders simultaneously by using batch picking. Here, they receive a group of orders to complete together before delivering them to the packaging station.