As a manufacturing business, have you ever thought about the logistics of storing and shipping products? This is usually done in a large space called a warehouse. It usually is a huge space carefully made to keep your inventory. The software used to make warehouse management more effective and efficient is called a warehouse management system.
In this blog post, we will learn what a warehouse management system is, its key features, benefits and challenges, and who uses a warehouse management system.
What Is a Warehouse Management System?
Warehouse management is the process of taking care of the movement and storage of goods in a warehouse. A warehouse management system is especially important for SME manufacturing businesses. It is because the SMEs are constantly growing very fast. They do require the tools that can manage the scaling. This system helps SMEs optimize their inventory and production operations. An effective warehouse management system can help you maintain efficient operations.
The warehouse management process starts when products arrive at your warehouse and continues until they are shipped to fulfil orders. It includes all the control and planning such as inventory tracking, order fulfillment scheduling, and space optimization. This helps you make sure your warehouse is operating at optimal capacity. Just like every system, this one too has several components. And for warehouse management to work properly, all the components need to work together.
What does a Warehouse Management System do?
A warehouse management system is a tool that gives complete control to the SMEs over the day-to-day management of their warehouse. It manages the stock storage and picking, packing and delivery of your goods. It also keeps track of the movement and location of the items in the warehouse. Additionally, it can also analyze sales, trends, and margins of your goods.
These systems form a part of an overall enterprise resource planning (ERP) system. They can help a business with the following:
- Data-driven: A warehouse management system will keep a check on every step of your procurement and inventory operations of you SMEs. It will collect useful data from each of these processes. This can help you get a better idea of what the predicted demand is, what your potential supply is, and how your daily operations are set up to match the two.
- Highly Integrated: Manufacturing businesses of small and medium size and scale often implement an ERP software to digitize their entire business. An effective warehouse management system will integrate well with your existing systems.
- Efficient: This system evaluates every step of your warehouse operation from the receipt of goods to the delivery and order fulfillment. Each step has a scope for improvement. A warehouse management system will help you do this.
Who Uses Warehouse Management Systems?
A warehouse management system is usually used by companies that have a warehouse or distribution centre. They need it for streamlining their storage. However, this software solution can be used by any business looking to improve their warehouse operations.
Every business tries to create a satisfactory experience for customers and build brand loyalty. For that, a business needs to have a streamlined structure for operations. The most important aspect of operations is effective warehouse and inventory management.
A warehouse management system can be used by:
- Manufacturers: Manufacturers often use a WMS to manage the storage and movement of raw materials and finished goods. They are better able to manage their inventory with the help of a warehouse management system.
- Wholesalers: Wholesalers often must deal with a huge number of goods. A WMS comes in handy in helping them efficiently manage their inventory.
- Distribution Centers: These businesses focus on storing goods and fulfilling orders for other businesses. A WMS is an important part of their business, and it helps them streamline their output.
- Third-Party Logistics (3PL) Providers: 3PL companies provide warehousing and logistics services to other companies. For that, they must use a WMS to manage their clients’ goods.
Key Benefits of Warehouse Management Systems
A warehouse management system can simplify your operations and make your tasks easier. If done properly, you can get many advantages of warehouse management for SME businesses.
Some advantages of WMS are as follows:
- Increased efficiency: Warehouse management can help you make the most of your space as well as human resources.
- Improved productivity: An effective warehouse inventory management system will also help you create processes and workflows that increase productivity at every step. It will help you remove inefficiencies and save time as you perfect each stage of your operations.
- Saved costs: With a good inventory management system for the warehouse in place, you will be able to identify parts of your operations that create unnecessary expenses. You can correct them quickly.
- Satisfied customers and partners: When your warehouse management is efficient, your entire supply chain benefits. This includes your suppliers as well as the final customer. It will also ensure that there are no delays in order fulfilment.
Types of Warehouse Management System
Different warehouse management systems have different functions. Each comes with its benefits and challenges. To find out which one suits your needs best, you need to understand the types of WMS.
Here are the main types of warehouse management systems:
-
Standalone Systems: These are standalone management apps. They operate independently and are a good fit for businesses with simple, straightforward needs.
-
ERP Modules: These modules are multifunctional and are part of a larger inventory management system for warehouses. They manage multiple aspects of a business, including warehousing.
-
Cloud-Based Systems: These kinds of WMS are accessible from anywhere. They offer flexibility and scalability. Cloud-based systems are a great choice for businesses that are growing or have multiple locations.
Key Features of Warehouse Management System
A warehouse management system comes with many features. Some of its most important features are:
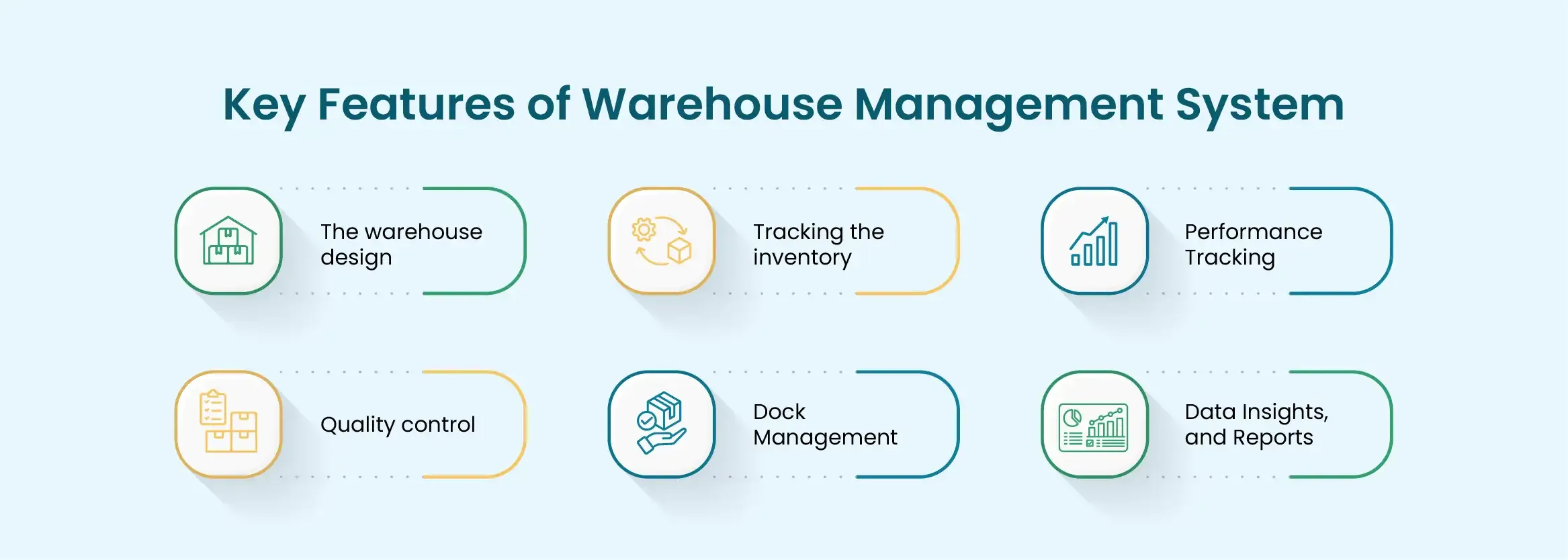
-
The warehouse design: An effective warehouse management system makes the most of your available warehouse space. It can help you make sure inventory is placed strategically.
-
Tracking the inventory: The warehouse management system you choose should be technically capable of inventory tracking. This will help you to get rid of the need for human intervention.
-
Performance Tracking: Warehouse inventory management systems also need to consider the human resources that manage day-to-day operations. The system can streamline goal setting and performance tracking of your employees.
-
Quality control: Picking, packing, and shipping are three of the most important processes in warehouse management. A good management system will make sure that every order is picked, packed, and shipped accurately.
-
Dock Management: WMS will make your deliveries easier. It can make sure that they are made in the right place, in the right quantity, and at the right time by the manufacturing facility.
-
Data Insights and Reports: Warehouse management software needs to be capable of analyzing all the data generated by your operational processes. You should choose a warehouse management system that provides you with in-depth reports and insights.
Inventory Management System vs Warehouse Management System
It can feel like Inventory Management System and Warehouse Management System are the same or similar but they both have very different uses.
Inventory management system
The inventory management system manages the movement of your inventory as a part of your operations. This includes keeping a record of how many products need to be ordered according to the forecasted demand. It is also about the system that is put into place to store these products, move them around within the warehouse for packaging, and pick the right ones to ship out. Inventory management includes more than just finished products. It also revolves around dealing with raw materials that are needed to create finished goods.
Warehouse Management System
Warehouse management, on the other hand, is a system that is in place to run the day-to-day operations of your warehouse. This includes not just the inventory part of it, but also staff management, warehouse layout, and design, overall monitoring, and reporting. Warehouse management systems are built to help business owners maximize the productivity and operational efficiency of their entire warehouse. But, inventory management is focused only on perfecting the inventory part of it.
Below is a table comparison of the Inventory Management System vs Warehouse Management System for an easier understanding.
Parameters | Inventory Management System | Warehouse Management System |
---|---|---|
Definition | A method for forecasting, ordering, receiving, and allocating stocks | The Warehouse Management System includes managing stock storage and picking and packing activities in a warehouse. |
Focus | Inventory Management System focuses on overall inventory levels and their statuses. | Tracks the movement and location of stock within the warehouse. |
Function | Determines to reorder based on demand and preferred stock levels. Shows the inventory record and inventory availability. | Streamline the tasks of a Warehouse. |
Tracking | Provides information to calculate sales trends, profit margins, etc. and tracks all the stock. | A WMS tracks where each type of stock resides within a warehouse. |
Challenges in Warehouse Management
Warehouse management is a useful tool in helping you increase the efficiency of your operations. However, there are often challenges you may face when trying to implement a warehouse management system.
Here are some challenges in warehouse management you need to watch out for:
- Warehouse Layout: A badly planned warehouse layout can lead to unwanted accidents and an inefficient flow of products.
- Inaccurate Planning: A core part of your warehouse management process is effective inventory management. You will face delayed shipments and unhappy customers if this is not done properly.
- Labour Costs: The cost of labour always needs to be balanced out with the productivity it can create for you. Streamlining warehouse management may help you reduce your costs.
How to choose the Right warehouse management system for small business
A Warehouse Inventory Management System can improve the operational efficiency of Small and Medium Enterprises (SMEs). SMEs have many tasks to deal with. It can include picking, packing, and shipping processes. A WMS can help your SMEs keep track of inventory as well as decrease the risk of overstocking or understocking.
But, considering the number of choices that are currently available in the market, how will you decide which is the best warehouse management system for small businesses? Here are some of the points that you need to keep in mind when choosing the right warehouse management software:
- Return on investment: When evaluating the right warehouse management system, make sure you keep the bigger picture in mind. Try to calculate the return on investment for implementing this system.
- Real-time data: The best warehouse management system for small businesses should provide you with real-time updates and alerts.
- Analytics and reporting: Make sure you evaluate the reporting capabilities of your warehouse management system. The software should be able to derive useful insights from your operations and workflows.
- Scalability: As a manufacturing company, you need to get tools and systems that can scale up when you need to. This will help you make sure that order fulfilment and customer satisfaction are never negatively impacted by growth.
Inventory and Warehouse Management with TranZact
From the many choices present in the market currently, it is challenging to pick a tool that will best suit your requirements. In this case, TranZact can be an ideal choice.
TranZact offers inventory management software which can help you take care of several parts of your warehouse. It provides real-time data, analysis and reports, and easy scalability. This can help you with a high ROI with optimum support for your business.
FAQs:
1. What is the difference between a warehouse management system and an inventory management system?
An inventory management system tracks the movement of stock in a particular warehouse, at all times. On the other hand, a warehouse management system looks at the entire day-to-day management of a warehouse. This includes everything from receiving, storing, picking, packing, and shipping the product.
2. What is the difference between inventory and stock?
Stock refers to the products that are already available to a seller. These products are ready to be sold to customers. Whereas, inventory refers to all the available resources. This includes raw materials, goods that are currently being manufactured and goods that are ready to be sold.
3. What is the difference between material management and warehouse management?
Material management focuses only on the raw materials that are used to develop finished goods. On the other hand, warehouse management is used to run a warehouse and all the processes within it.
4. Why is a Warehouse Management System (WMS) essential for manufacturing businesses?
A WMS is important for manufacturing businesses because it can improve storage space, streamline picking and packing processes, manage staff, and ensure timely and accurate delivery of products.
5. How does an efficient Warehouse Management System (WMS) contribute to cost savings?
An efficient WMS streamlines warehouse management operations. This reduces the need for manual follow-ups, and checking. A WMS can reduce operational costs by improving storage layouts, inventory tracking, and order fulfilment processes.
6. What are the key features to look for when selecting a Warehouse Management System?
When selecting a WMS, you should consider features like real-time data tracking, analytics, reports, scalability, and integration with other systems. The system should also offer tools for perfecting warehouse layout and tracking inventory with technology like a barcode scanner.
7. What are some essential resources for warehouse managers to perfect operations?
Key resources for warehouse managers include Warehouse Management Systems (WMS) that offer real-time data tracking and analytics. It also includes inventory management software for correct stock control, barcode scanners and RFID technology.
8. What are the main 4 functions of warehouse management?
The 4 main functions of warehouse management are understanding the objective of the system, coordinated management of the warehouse, its adaptability and customer-centric approach.
9. Which software is used for warehouse management?
Currently, there are many softwares available in the market. Some of the popular ones are TranZact, Zoho ERP, Oracle etc. TranZact can be a good option if you are looking for a system that focuses on integration and can become a one-stop solution for all your operations needs.
10. What is warehouse inventory management?
Warehouse inventory management is the process, which helps businesses organize, track and handle their goods, particularly in warehouses. It involves tasks like receiving, maintaining, tracking, packing, and shipping out orders.