A good warehouse layout can improve workflow and shipping times. However, poor execution can harm logistics and delivery times. It is best to redesign the layout to increase efficiency, improve workflow, and create a safer work environment. Consider elements such as space utilization, operations, and revenue to develop layouts for strategic business operations. Finding a warehouse layout that perfectly fits your business needs can be challenging.
You can use the tips and suggestions provided below for better efficiency and effectiveness in warehouse layout.
Tips for Designing Your Warehouse Layout
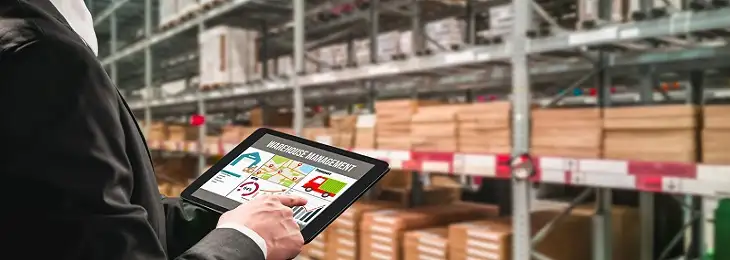
The warehouse layout design setup requires various elements in line with each other. Creating the layout requires having a well-defined game plan and following a set of actions to find the ideal layout plan meeting the business needs.
Here are the top tips you can keep in mind before designing the warehouse layout plan-
1. Map Out the Warehouse Layout
Create a plan, warehouse layout, or blueprint using current or new maps on the design software. Get the help of a warehouse design and layout specialist to improve the design as per business demands.
Take accurate measurements of your workspace and set up different sections, workflow directions, and operating zones. To decide on any adjustments, include space dimensions such as building height. Once the map is in place, maximize your space by making it clear and well-organized.
2. Plan Out Space Warehouse Layout Optimization
The amount of available space, including storage, workflow zones, and equipment, decides your warehouse layout. Consider grouping together or putting storage in corridors to save space.
Vertical space is important for improving storage capacity and increasing available space. Calculate the area in your warehouse and devote 22-27% of it to goods warehousing. Make the best use of the available area by avoiding duplicating storage, work environment, and technology.
By reducing office areas and empty pallets, companies can make better use of warehouse space, improve inventory visibility, save travel time, and increase operation productivity.
3. Choosing the Right Equipment
Warehouse operations vary in size, space, and storage, calling for a wide range of equipment. It affects corridor space and transportation of goods requirements.
Identifying the right equipment in warehouse layouts has an impact on the design of layouts and boosts efficiency.
Two important types of equipment involved in warehouse planning include -
- Forklift
Forklifts are necessary for warehouse operations as they move bulky goods and bundles. Leasing a forklift can be affordable, but proper safety measures are necessary to prevent damage.
- Pallet Jack
Pallet jacks serve as essential industrial tools for transferring tiny commodities. They are essential for safety and adequate training and are available in mechanical and motorized variants. Proper usage of technology and equipment and personnel training is important to maintain a smooth workflow.
4. Test the Workhouse Plan and Make the Required Changes
Before planning or changing your warehouse, perform a test by measuring the new layout, marking the boundaries, and walking through it.
Employers should test the new design using the technology and equipment. Keep track of responses and make changes as necessary.
5. Consider Budget
Review business requirements, finances, and warehouse design effectively. Consider the most appropriate and cost-effective warehouse solution within the defined budget to meet the goals and organization demands.
6. Ensure the Flow of Goods
Create an organized arrangement for the warehouse to ensure the smooth movement of goods, workers, and equipment.
7. Accessibility to All Workstations/ Areas
Design a warehouse structure that allows staff members to travel easily and keep track of inventory requirements. It improves efficiency and reduces the processing time of orders.
8. Well-Trained Personnel Involved
Designing a warehouse layout based on workforce needs, training, and shift timings guarantees productivity. It does not limit the workforce and securely accepts new personnel into the workspace atmosphere.
9. Meet Authority Guidelines
Following local authorities' rules for security, safeguarding assets, preventing penalties, and legal challenges must be considered when planning a warehouse plan.
10. Throughput
In a warehouse, throughput monitors the flow of goods through operations like receiving raw materials, storing, picking, packaging, and transporting goods.
Read Also: Understanding Backorders: What They Are, Causes and Solutions
Warehouse Layout Designs Suggestions

Warehouse plan optimization enhances business operations. Here are the top three types of warehouse layouts opted for by the businesses -
1. U-Shaped Design
A U-shaped warehouse plan is suitable for small, simple infrastructure. It is separated into load and shipment areas and a reception space after loading and picking areas following shipping. It has flexible and stable storage for easy administration.
2. L-Shaped Design
The L-shaped warehouse layout includes loading and receiving spaces on one end, shipment and pickup facilities on the other side, and plenty of inventory storage capacity.
3. I-Shaped Design
The I-shaped layout is appropriate for massive production warehouses, with loading and unloading spaces on one side and shipment areas on the opposite side. The storage area is located in the center. This arrangement allows easy pickup of large quantities of goods, yet it requires full factory transportation.
Read Also: Maximum Stock Level: Definition and Calculation
Effective Warehouse Layout Design Tips
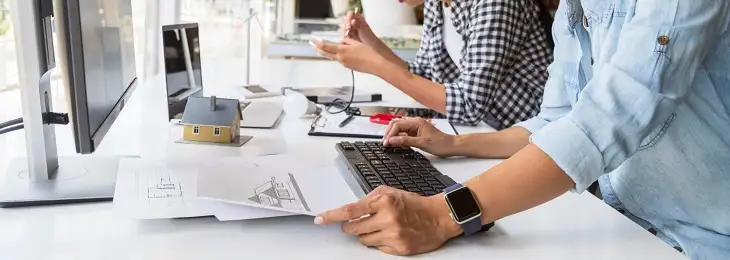
Developing a warehouse plan or layout that is one size fits all is difficult. However, here are the universal effective warehouse layout design tips -
1. Set Up Spaces Between Loading and Unloading Zones
Warehouse loading and unloading areas are either connected or separate. Built-in sections provide access docking places for vehicles to connect and unload merchandise.
Independent areas require a two-step design, with a forklift for product transfer to the storage facility and reception area.
2. A Separate Reception Area
The reception room, also known as the staging area, is important for product organizing, distribution, and quality assurance. Separate it from the rest of the warehouse to allow for accurate inspections and to reduce delays.
3. Organize Storage Spaces
Vertical storage is preferable; however, stacking is only appropriate for heavy loads and stiff containers. Warehouse layout optimization can result in quicker turnaround times and greater satisfied clients.
4. Separate Picking Area
Separate picking components for preparing orders frequently occur in shipment warehouses. Place them in or near the storage spaces to avoid wasting time looking for them.
Improve Warehouse Designing With TranZact
The ideal warehouse layout plan for your business facility will improve the utilization of resources. Consider the factors and the tips discussed above to design the layout to promote productivity and work quality and to increase the order delivery rates. TranZact provides the best warehouse management solutions and software, including cloud inventory modules for small businesses, to help them properly manage inventory.
FAQs on Warehouse Layout
1. How can the warehouse layout be improved?
The warehouse layout can be improved by using a suitable pallet size, choosing the correct storage handling and racking mechanism, selecting the right vehicle for every process, etc.
2. How to do space optimization in a warehouse?
To optimize space in a warehouse, build an upper-level area beyond floor level, reduce aisle thickness in the racking area, add vertical racking, change the storage mechanism, and go for underlying space.
3. What makes a good warehouse layout?
A good warehouse layout includes various factors, like the ease of loading and unloading the products on one end of the process, storage capacities in the middle, and the shipping area on the other end of the process.
4. What is the importance of warehouse optimization?
Warehouse optimization allows the team members to develop a more positive work atmosphere for the workforce; it helps handle shipping timely and helps properly organize the production process.
5. What are 5 of the most important KPIs (key performance indicators) in warehouse management?
The five most important KPIs of a successful warehouse management system include:
- inventory turnover,
- inventory accuracy,
- effective receiving stock,
- picking and packing orders
- CCOT (Customer Cycle Order Time) for customer product satisfaction metrics.
6. What are the steps involved in warehouse layout design?
Some steps of warehouse layout include:
- Outlining warehouse workflow
- Defining workstations and departments
- Streamlining storage
- Setting up a warehouse management system
- Managing consumer feedback
- Managing product packing and picking areas.
7. What are the 3 warehouse layout options?
The three main types of warehouse layout options for businesses include I-shaped, U-Shaped, and L-shaped options to organize inventory systems.